Electronic Contract Manufacturer
Incoming Inspection
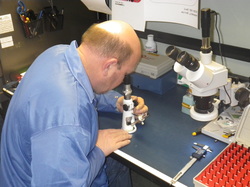
Prior to releasing to the stock room or production floor, custom bought parts are routed to our Incoming Inspection Stations. Here the parts are thoroughly checked against part specific Receiving Inspection Check Lists. All Rejected Material is Red Tagged and Quarantined to ensure it doesn't get used in customer products. Inspections range from the more complicated PCB microsection to paint thickness.
The following is a list of our inspection tools.
The following is a list of our inspection tools.
- 100X Microsection Microscope
- 30X Microscope
- Coating Thickness Gauge
- Vernier Calipers
- Micrometers
- Microfinish Comparator
- Pin Gauges
- Radius Gauges
- Angle Gauges
- Test Fit Samples (Golden Product Samples)
In-Process and Final Inspection/Test
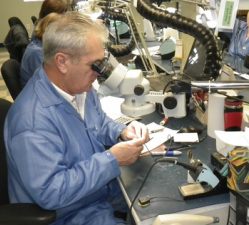
All manufactured assemblies are inspected and tested as defined by documented Manufacturing Instructions. Solder joints and crimps are 100% inspected under magnification by qualified Inspectors. Crimp Pull Tests are performed before every crimping job to validate the crimping process. All Rejected Material is Red Tagged and Quarantined to ensure it doesn't get used in customer products.
Workmanship Standards
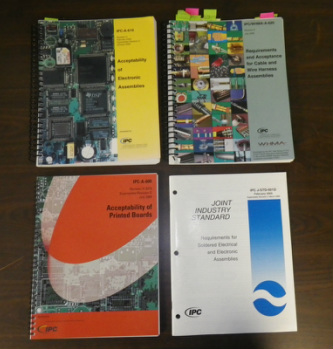
At Precision Outsourcing Inc., Quality and Customer Satisfaction is our top priority. To ensure high quality, only trained personnel are used to build customer products. Our manufacturing staff is trained to IPC-A-610, IPC/WHMA-A-620 & IPC J-STD-001 Class 3 standards. All customer products are built to these standards unless superseded by customer supplied standards. In order to ensure repeatability in producing customer products, we use Controlled Manufacturing Instructions and Inspection/Test Sheets either supplied by our customers or created by us.
ESD
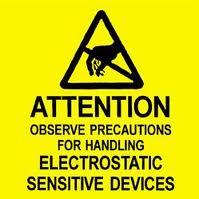
We manufacture ESD sensitive assemblies in an ESD controlled environment with grounded ESD mats. All personnel working in the ESD controlled areas wear ESD lab coats and grounding wrist straps and are trained in the handling and packaging of ESD sensitive materials. Wrist straps are tested and the results logged before every job. Access to ESD controlled areas and ESD sensitive materials is limited to ESD trained personnel.
Documentation
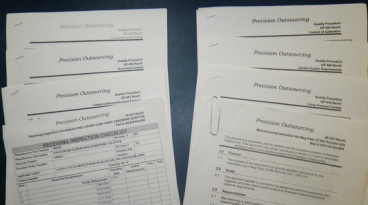
Our Document Control System ensures that all controlled documentation used in the operation of Precision Outsourcing Inc. is maintained under revision control & only the latest revision is used. Obsolete revisions are archived and stored indefinitely. Controlled Docs include quality procedures, administration procedures, manufacturing instructions, inspection/test procedures, calibration procedures, customer supplied documents, etc. All inspection data from Incoming Inspection to Final Inspection/Test is documented and stored indefinitely.
Calibration
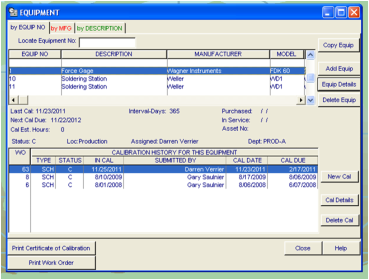
All equipment used in the manufacturing and testing of customer products is entered in our Calibration database and assigned a calibration cycle defined by its intensity of use. Calibrated equipment is clearly marked with a calibration label and uncalibrated equipment is segregated from the manufacturing floor.
First Article
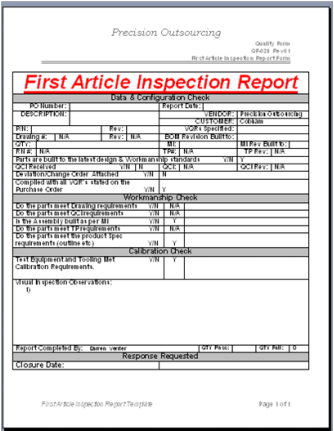
All new products go through our First Article Process before the first production run. For this process, only a small quantity of assemblies are produced. This allows us to identify any discrepancies in the customer documentation package, suggest improvements or create manufacturing aids.